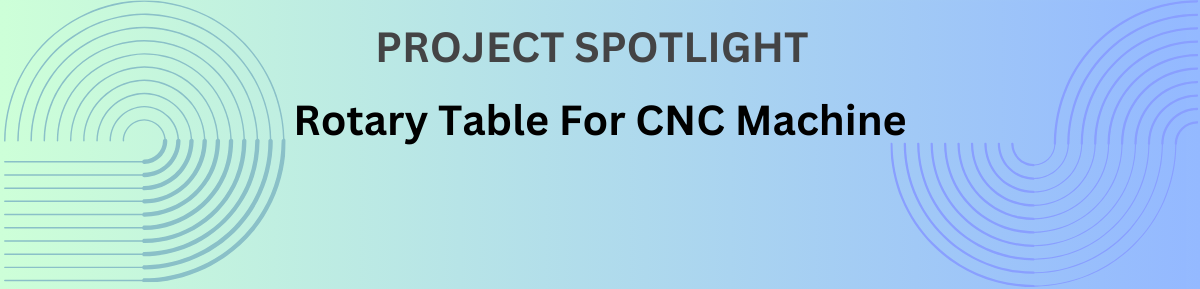
Project Overview
Designed and developed a Raspberry Pi-based control system for managing a single-axis rotary table. The system communicates with a Variable Frequency Drive (VFD) using EtherCAT protocol, enabling real-time control of rotary table operations. This solution enhances automation and improves operational efficiency.
Key Features
- • Raspberry Pi Control System: Cost-effective and scalable controller solution.
- • EtherCAT Communication: High-speed, real-time data exchange with the VFD.
- • VFD Motor Control: Precision control over speed, direction, and acceleration.
- • User-Friendly Interface: Graphical interface for easy monitoring and adjustments.
- • Real-Time Data Monitoring: Continuous diagnostics and data logging for predictive maintenance.
Business Impact
- Increased Operational Efficiency: Automation reduces manual intervention, speeding up production cycles and improving accuracy.
- Cost Savings: Leveraged affordable hardware, reducing overall system costs.
- Scalability: Easily adaptable for additional features or multiple axis control.
- Enhanced Product Quality: Improved precision ensures consistent product outcomes.
- Reduced Time-to-Market: Accelerated development cycle using open-source platforms, enabling faster deployment.
This platform not only enhances efficiency and reduces costs but also empowers businesses to scale effectively, ensuring consistent product quality and rapid market readiness.